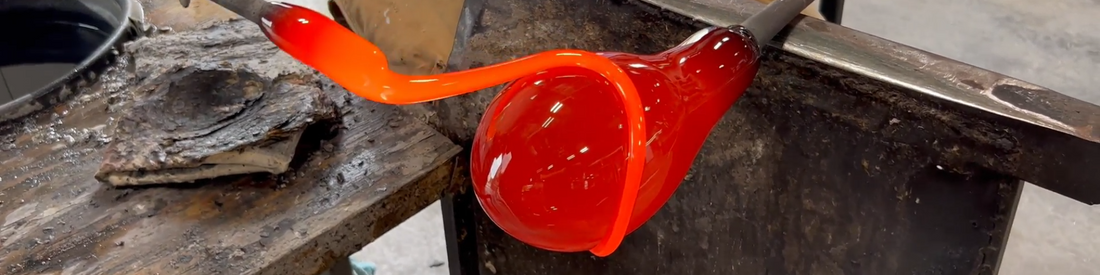
Inside the Studio: Your Glass Step by Step
At Bicycle Glass Co., every light we make carries the mark of a human hand—and a whole lot of heat.
To us, lighting isn’t just about utility, it’s about creating something that carries meaning. Every sconce, pendant, and chandelier we make is shaped by hand from 100% recycled glass, using age-old glassblowing techniques.
So, how do we turn post-consumer glass into glowing works of art? Let’s take you behind the scenes into our hotshop, where the magic happens.
Step 1: Gathering the Glass
The process begins at the furnace, where recycled glass is melted down into a glowing, molten state at around 2000°F. Using a 5-foot-long steel blowpipe, one of our glassblowers gathers a glob of glass from the furnace. It's just that short pipe between the glassblower and a crucible of molten material.
This step alone takes serious control and confidence, built through years of experience. Once the glass is gathered, it immediately begins to cool down and the clock starts ticking.

A gather of glass on the end of a blowpipe. The blowpipe is being cooled off in a special barrel of water so it can be handled safely.
Step 2: Shaping the Bubble
With the glass gathered on the pipe, the shaping process begins. We use a mix of traditional tools and simple materials—like blocks of wood, steel jacks, and even wet newspaper, to shape the glass into a uniform shape. The gaffer then blows into the pipe to form a bubble in the middle of the glass, expanding the globe.
Each team member works in sync to reheat, shape, and blow the glass just enough to get the perfect size and thickness for the intended design.

A gather of glass being shaped with wet newspaper.
Step 3: Adding Signature Style
At this point the basic shape is ready, but now comes the artistic detail. Every lighting shape we offer has its own unique personality, and that’s created by hand on each globe.
Swell Series: We add a thick “bit” of molten glass in a figure eight curve on the surface of the globe.
Lunar Series: A special powder is sprinkled on the hot glass, causing bubbles to develop across the surface.
Spun Series: A thin "bit" is applied to the glass as the piece is spun to create a natural webbing look. This pattern can only be made by hand and by feel.
Each globe is slightly unique, with the markings of its creation visible in subtle ripples, bubbles, and textures.

Applying a Swell "bit" to the outside of a glass bubble.
Step 4: Into the Annealer
When the shaping is complete, the glass is placed into an annealer—a type of kiln that slowly cools the glass over several hours (sometimes overnight). This step is critical to avoid cracks or stress in the material. It allows the molecules in the glass to stabilize, giving each piece strength and durability that will last for decades.

Loading a 767 Spun globe into the Bicycle Glass conveyor annealer.
Why We Do It This Way
Handblown glass takes longer. It’s harder to master. And it’s never exactly the same twice.
But that’s the point.
We believe in making things that last—and in honoring the craft that makes them special. Working with 100% recycled glass presents its own set of challenges, from air bubbles to temperature quirks, but it’s part of our commitment to sustainability and meaningful design.

Closeup of the Swell glass style, Lunar glass style and Spun glass style.
See the Process in Action
Want to see the hotshop for yourself? We filmed a quick video inside our studio to give you a glimpse of the process. You won’t catch every step (some secrets are worth keeping!), but you will see the fire, the teamwork, and the care that goes into every piece we make. Thanks for taking the time to go behind the scenes with us—we're proud to share the journey with you.
Watch the Studio Tour 👇